Механика машина основы управления: Механика машина основы управления. Как пользоваться механической коробкой передач. Зачем уроки вождения на механике для начинающих включают в себя умение «дауншифтить»
Автомобили с МКПП автошколы «Перспектива»
В нашей автошколе Вы можете пройти обучение вождению на автомобиле с механической коробкой переключения передач. Стоит отметить, что «механика» обладает своими особенностями. Так, она предполагает самостоятельное переключение скоростей водителем и заставляет его быть более активным за рулем. Как правило, новичкам этот процесс дается весьма непросто. Он требует понимания всех нюансов устройства трансмиссии, соблюдения последовательности переключения скоростей движения, знания правил нажатия педали сцепления, особенностей применения пониженных и повышенных скоростей в различных условиях дорожного движения и др. Вместе с тем, при существующих недостатках нельзя не отметить положительные стороны.
Достоинства МКПП:
- абсолютный контроль над автомобилем;
- высокий КПД;
- экономичное потребление топлива;
- возможность блокировки движения с применением ручного тормоза;
- простота конструкции и относительная дешевизна обслуживания;
- большой срок службы;
- возможность буксировки машины без привлечения эвакуатора.
Минусы механики:
- сложность управления;
- возможность перегрузки двигателя при некорректном переключении передач;
- быстрая утомляемость водителя во время езды в городских заторах;
- более узкий круг поиска при выборе и покупке авто.
Обучение на автомобилях с МКПП
Опытные инструкторы нашей школы помогут Вам в полной мере освоить все особенности управления автомобилей на механике, что позволит уверенно чувствовать себя за их рулем в любых обстоятельствах. Во время занятий ученики не только получают базовые знания и навыки управления транспортным средством, в частности, переключение скоростей коробки, но и изучают устройство данного вида трансмиссии, основные правила ее грамотной эксплуатации. Их учат выполнять все основные элементы маневрирования, правильно двигаться в условиях загруженного городского движения, тормозить и трогаться на светофорах и в пробках, не останавливая двигатель, переключать скорости в экстренных ситуациях.
Важен тот факт, что если ученик освоил управление автомобиля, оборудованного механической трансмиссией, он всегда сможет управлять машиной, оснащенной «автоматом». В том время, как обратная ситуация невозможна: имея водительское удостоверение с отметкой о праве управления автомобилем с АКПП, нельзя садиться за руль «механики». Именно поэтому уроки вождения на МКПП – прерогатива профессионалов высокого класса.
Не заводится машина | Основные причины и методы их устранения
Причин отчего мотор не подает признаков жизни великое множество, а иногда одна проблема тянет за собой другую, и сразу сложно разобраться почему машина превратилась в недвижимость. Мы разберем самые частые причины не касаясь нюансов.
Стартер. Стартер — это небольшой электродвигатель, который передает коленчатому валу крутящий момент, необходимый для воспламенения топлива.
Если после поворота ключа (или нажатия кнопки старта двигателя) ничего не происходит или раздаются нехарактерные щелчки, то скорее всего проблема в стартере.
Причины из-за которых не заводится машина в этом случае могут быть разными: от износа щеток или подшипников до окислившихся контактов и замыкания проводки. На месте вы сможете проверить только контакты от аккумулятора, и сам аккумулятор — может быть он вышел из строя. Остальное лучше доверить специалистам. Стоимость ремонта зависит от того, что случилось со стартером. Может быть его удастся починить или придется заменить целиком.
Генератор или аккумулятор. Если в двух словах, то генератор — это устройство, превращающее часть энергии двигателя в накопленный заряд аккумулятора. Неисправный генератор не заряжает (или заряжает недостаточно) аккумулятор, у которого не хватает заряда, чтобы запустить стартер. Старый аккумулятор плохо держит заряд и быстро разряжается, особенно на морозе. Обычно проблема в чем-то одном.
Аккумулятор может быть разряжен «в ноль» и тогда стартер не будет крутиться, а панель приборов не включится. Если напряжение еще есть, то машина предупредит вас о разряженной батарее пиктограммой на панели приборов. Автомобиль может завестись после того как его «прикурили» от другого, но вы почувствуете, что генератор заряжает аккумулятор в пол силы и после стоянки в машине снова нет «тока».
Если генератор сломался, то единственная дорога — в сервис. Кстати, проверьте ремень генератора, если знаете, где он расположен. Возможно, проблема в нем. Если видите, что его оборвало, заказывайте эвакуатор. В современных моторах на этом ремне работает система охлаждения и двигатель можно перегреть, если поехать своим ходом. Старую батарею по силам заменить самому, предварительно проверив надежность контактов на клеммах и линию проводов от генератора к аккумулятору.
Свечи зажигания. Двигатель может не заводиться из-за отложений на свечах из-за которых они работают некорректно или вовсе не дают искру. Обычно такое происходит по вине топлива плохого качества. Еще варианты: износ электрода или свечного разъема.
Система подачи топлива. Может быть неисправен топливный насос — сгорел или проблемы с проводкой. Само по себе это устройство редко ломается. Чаще так бывает из-за привычки ездить «на парах», заливая в бак минимум. Топливные насосы охлаждаются, «купаясь» в топливе, а если его мало, то перегреваются и работают на износ.
Другая причина: поврежден топливный шланг. В этом случае в машине обычно пахнет горючим. Иногда сильно засорен топливный фильтр, который перестает быть фильтрующим элементом и превращается в заглушку.
ЭБУ.Электронный блок управления двигателем может быть неисправен — из-за этого запустить двигатель не получается. Часто такое бывает, когда коробка ЭБУ в коррозии и контакты на плате внутри повреждены. В некоторых моделях машин блок управления конструктивно неудачно расположен. Он начинает ржаветь через пару лет эксплуатации, а потом начинаются проблемы с пуском мотора.
Так как автомобиль — сложное устройство, состоящее из множества элементов, то слабых мест может быть великое множество.
Перечислим другие возможные проблемы из-за которых машина может не заводиться:
- недостаточное давление в цилиндрах;
- негерметичность проводов зажигания;
- неисправные датчики положения коленвала, распредвала, холостого хода, кислорода;
- проблемы с цепью или ремнем ГРМ;
- неисправность катушки зажигания;
- или банально кончилось топливо, а вы не заметили, или врет показатель его уровня.
Почему не заводится автомобиль зимой?
В зимнее время все болячки автомобиля вылезают наружу. Иногда приходится узнавать о поломках утром у холодной машины. Вот несколько причин почему она не заводится, чтобы сэкономить вам время.
Разрядился аккумулятор. Стартер крутит медленно или машина вообще не подает признаков жизни. Это одна из самых частых проблем с запуском двигателя зимой. Зимой старые аккумуляторы разряжаются быстрее. Особенно если в цепи машины есть источники потребления в виде противоугонной системы или видеорегистратора. Меняйте батарею на новую и можно большего объема — это не навредит. Главное, чтобы аккумулятор был такого же размера.
Замерзло топливо. Так бывает, если автомобиль дизельный. Специальные присадки в солярке не дают ей замерзнуть в морозы, но не всегда эти добавки работают, а иногда сами владельцы забывают, что наступила зима. Работоспособность топливной системы может быть нарушена из-за замерзшей в ней воды из некачественного топлива. Эвакуация в теплое помещение обычно помогает решить проблему.
Свечи накаливания пора менять. Зимой чаще выходят из строя свечи накаливания. Тут выход один — менять и лучше комплектом.
Моторное масло загустело. На морозе многие масла имеют неприятное свойство густеть, тогда стартер не может провернуть вязкую массу. На случай морозов заливайте сезонное масло с вязкостью 0W или 5W, а еще ищите отзывы реальных автовладельцев о масле, которое они используют в холода. Отзывы важнее надписей на этикетках, тем более у всех производителей есть хвалебные слова про минимальную восприимчивость их лубрикантов к низким температурам.
Вместо вывода
Причины из-за которых не заводится авто могут быть самыми разными, но определить настоящую и решить проблему смогут только специалисты. В официальном дилере десятка автомобильных марок FAVORIT MOTORS проверка автомобиля занимает минимум времени. Диагностику проводят на профессиональном оборудовании, и если надо используют специальные «дилерские» инструменты. Стоимость работы обговаривается с водителем заранее и не меняется. На любой ремонт есть гарантия.
Кафедра механики — ФГБОУ ВО «Магнитогорский государственный технический университет им.
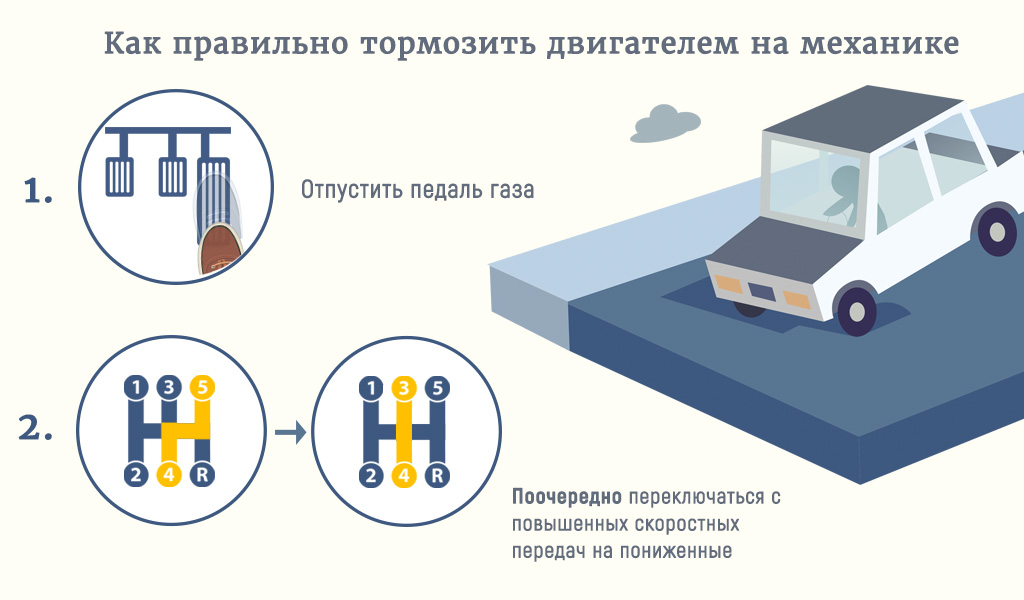
Савинов А.С.
Заведующий кафедрой: Савинов Александр Сергеевич, директор Института металлургии, машиностроения и материалообработки, доктор технических наук
Адрес: пр. Ленина, 38 (УК №1), ауд. 324 (зав. кафедрой), ауд. 315, 327 (преподавательские), ауд. 316 а,318 (препараторская), ауд. 029, 031, 082 (учебная лаборатория), ауд. 323 (лаборатория компьютерного моделирования), ауд. 305а (лаборатория динамических процессов механического оборудования)
Телефоны: +7 (3519) 29-85-18 (зав. кафедрой), +7 (3519) 29-84-27 (преподавательские), +7 (3519) 29-85-18 (препараторская)
Кафедра осуществляет подготовку будущих специалистов и бакалавров по дисциплинам: Сопротивление материалов, Теоретическая механика, Механика, Прикладная механика, Техническая механика, Детали машин и основы конструирования, Теория механизмов и машин, Детали машин, Строительная механика.
На кафедре обучаются студенты 1, 2, 3, 4 курсов всех факультетов и институтов.
Теоретическая механика, сопротивление материалов, теория механизмов и машин, механика, прикладная механика, детали машин, строительная механика формируют теоретическую базу инженерного мышления специалистов и бакалавров различных профилей. Число аудиторных часов, отведенных на изучение этих важных дисциплин, постоянно уменьшается, в связи с этим повышается роль самостоятельной работы обучающихся, индивидуального подхода преподавателя к каждому обучающемуся.
Коллектив кафедры прилагает огромные усилия к тому, чтобы максимально облегчить обучающимся усвоение важных для их технического образования курсов: преподаватели кафедры используют в процессе обучения компьютерные технологии, привлекают уже на первом курсе к учебно-исследовательским работам. Ежегодно кафедра проводит олимпиады, издается большое количество учебных и методических пособий , электронных ресурсов.
На кафедре механики работают 11 высокопрофессиональных преподавателей: 2 доктора технических наук, 1 профессор, 6 кандидатов технических наук, 5 доцентов ,5 старших преподавателей.
Судомеханический факультет — Балтийская государственная академия рыбопромыслового флота
В настоящее время кафедра выпускает бакалавров по специальности «Холодильная, криогенная техника и системы жизнеобеспечения», осуществляет подготовку аспирантов, проводит технические и научно-исследовательские разработки.
Квалификация: бакалавр.
Форма и срок обучения: очная — 4 года, заочная — 5 лет, заочная сокращенная — 4 года.
Принимаются юноши и девушки.
По данному направлению подготовки возможно обучение по сокращенной форме. Срок обучения: очная — 3 года, очная и очно-заочная — 4 года.
Кафедра постоянно совершенствует качество процесса подготовки выпускников. Проводятся смотры успеваемости и посещаемости курсантов, контролируется качество выполнения дипломных и курсовых проектов, курсовых курсантских научно-исследовательских работ. Совершенствуются лабораторные работы.
Курсантов старших курсов вовлекают в творческий процесс при подготовке учебных пособий. Вводятся новые, наиболее актуальные, курсы по выбору.
На кафедре внедрена система комплексной компьютеризации учебного процесса. Используются компьютерные мультимедийные средства при чтении лекций, разрабатываются компьютерные конспекты лекций, демонстрационные и иллюстрированные материалы на компьютерных носителях, читается курс Тренажерной подготовки на компьютерных тренажерах, разработанных кафедрой и ЗАО «Транзас». Постоянно совершенствуется материальная база кафедры за последние 2 года: приобретена двухступенчатая холодильная установка с рассольной системой охлаждения; ведется монтаж современного центра по исследованию холодильных машин систем кондиционирования воздуха.
Сферы профессиональной деятельности выпускника
- — специалисты по холодильной технике;
- — научно-исследовательские и проектные организации;
- — предприятия, занимающиеся эксплуатацией, монтажом и ремонтом холодильного оборудования;
- — машины, установки, двигатели и аппараты по производству, преобразованию и потреблению различных форм энергии, в том числе: теплообменные аппараты, системы кондиционирования, холодильные установки;
- — газовые инженеры.
На кафедре читаются дисциплины
- — Авто CAD
- — Автоматизация СХУ
- — Введение в специальность
- — Математическое моделирование в расчетах на ЭВМ
- — Научные основы криологии
- — Низкотемпературные машины
- — Основы автоматизированного проектирования
- — Основы теории кондиционирования воздуха
- — Приборы и техника измерений
- — Программирование САПР ХУ
- — Ремонт судовых холодильных установок
- — Системы динамического охлаждения и отопления, комфортное жизнеобеспечение
- — Судовые холодильные установки
- — Судовые холодильные установки и системы кондиционирования воздуха
- — Теоретические основы холодильной техники
- — Теория и расчет циклов криогенных систем
- — Теплообменные аппараты холодильных установок
- — Техническая эксплуатация СХУ
- — Тренажерный практикум
- — Холодильная технология рыбных продуктов
- — Хладагенты и хладоносители
Обучение по этой специальности осуществляется по основным образовательным программам подготовки, предусматривающим изучение курсантами следующих циклов дисциплин:
- — общие гуманитарные и социально-экономические;
- — общие математические и естественнонаучные;
- — общепрофессиональные;
- — специальные дисциплины.
Бакалавриат факультета электротехники и автоматики
Подготовка бакалавров осуществляется по двум направлениям:
Управление в технических системах
Руководитель направления – д.т.н., профессор Путов Виктор Владимирович
Образовательная программа реализуется двумя выпускающими кафедрами:
Профили подготовки бакалавров:
- Системы и технические средства автоматизации и управления;
- Управление судовыми электроэнергетическими системами и автоматика судов;
- Корабельные системы управления.
При обучении в бакалавриате по данному направлению студенты, наряду с изучением естественнонаучных (математики, физики, теоретической механики, информатики и др.), гуманитарных и социально-экономических дисциплин, получают знания и практические навыки в таких областях, как теоретическая электротехника, электроника, прикладная механика, инженерная и компьютерная графика, программирование и основы алгоритмизации, вычислительные машины системы и сети, метрология, силовая электроника, электрические машины, теория электропривода, теория автоматического управления, элементы и устройства систем управления, микропроцессорные устройства, компьютерное проектирование систем и устройств, динамика подвижных объектов, надежность и техническая диагностика систем и устройств, моделирование систем управления и другие.
Выпускникам бакалавриата присваивается степень бакалавра техники и технологий по направлению «Управление в технических системах».
Электроэнергетика и электротехника
Руководитель направления – к.т.н., доцент Белов Михаил Петрович
Образовательная программа реализуется двумя выпускающими кафедрами:
Профили подготовки бакалавров:
- Электротехнологические установки и системы;
- Электропривод и автоматика;
- Электрооборудование и автоматика.
При обучении в бакалавриате по данному направлению студенты, наряду с изучением естественнонаучных (математики, физики, теоретической механики, информатики и др.), гуманитарных и социально-экономических дисциплин, получают знания и практические навыки в таких областях, как теоретическая электротехника, электроника, прикладная механика, инженерная и компьютерная графика, программирование и основы алгоритмизации, вычислительные машины системы и сети, метрология, электрические машины, электрические и электронные аппараты, микропроцессорные устройства, теория электропривода, теория автоматического управления, автоматизированное проектирование и другие. Также, в зависимости от выбранной специализации, студенты проходят подготовку в области электромеханики, либо систем автоматизации и электропривода, либо электротехнологий.
Выпускникам бакалавриата присваивается степень бакалавра техники и технологий по направлению «Электроэнергетика и электротехника».
Ниже представлен список лучших выпускников бакалавриата за последние годы по направлениям «Управление в технических системах» и «Электроэнергетика и электротехника».
Аннотации ВКР бакалавров 2016 г.
Аннотации ВКР бакалавров 2017 г.
Аннотации ВКР бакалавров 2019 г.
Cессия, аттестация, посещение занятий | Санкт-Петербургский горный университет
Сведения об успеваемости студентов
Курс 3, Механико-машиностроительный факультет, группа МНМ-18, осенний семестр 2020/2021 учебного года
* — дисциплина по выбору или факультативная дисциплина
Номер документа | Механика материалов и основы конструирования | Правоведение* | Теория и технология термической и химико-термической обработки | Теория механизмов и машин | Экология | Физическая культура и спорт | Механика материалов и основы конструирования | Защита интеллектуальной собственности и патентоведение | Физика прочности и механика разрушения | Военная подготовка* | Безопасность жизнедеятельности | Методы исследования материалов и процессов | Механические и физические свойства материалов | Теория и технология термической и химико-термической обработки |
---|---|---|---|---|---|---|---|---|---|---|---|---|---|---|
25.![]() | 23.12.2020 | 23.12.2020 | 23.12.2020 | 23.12.2020 | 25.12.2020 | 23.12.2020 | 23.12.2020 | 25.12.2020 | 22.12.2020 | 26.12.2020 | 15.01.2021 | 12.01.2021 | 30.12.2020 | |
72 час. | 72 час. | 72 час. | 72 час. | 9 час. | 108 час. | 108 час. | 108 час. | 108 час. | 144 час. | 144 час. | 91 час. | |||
зачет | зачет | зачет | зачет | зачет | зачет | КР | д/зачет | д/зачет | д/зачет | экзамен | экзамен | зачет | зачет | |
180024 | зачет | зачет | зачет | зачет | зачет | зачет | хор. | удовл. | хор. | хор. | хор. | хор. | хор. | |
180671 | зачет | зачет | зачет | зачет | зачет | зачет | хор.![]() | хор. | хор. | хор. | хор. | хор. | хор. | |
180672 | зачет | зачет | зачет | зачет | зачет | зачет | хор. | удовл. | удовл. | удовл. | удовл. | хор. | удовл. | |
180673 | зачет | зачет | зачет | зачет | зачет | зачет | отл. | отл. | хор. | удовл. | отл. | отл. | отл. | хор. |
180674 | зачет | зачет | зачет | зачет | зачет | зачет | отл. | хор. | хор. | отл. | удовл. | удовл. | хор. | |
180675 | зачет | зачет | зачет | зачет | зачет | зачет | отл. | отл. | отл. | хор. | хор. | отл. | отл. | |
180676 | зачет | зачет | зачет | зачет | зачет | зачет | хор.![]() | хор. | отл. | хор. | удовл. | отл. | удовл. | |
180678 | зачет | зачет | зачет | зачет | зачет | зачет | отл. | отл. | отл. | отл. | отл. | отл. | отл. | |
180684 | зачет | зачет | зачет | зачет | зачет | зачет | хор. | отл. | хор. | отл. | отл. | хор. | хор. | |
180741 | зачет | зачет | зачет | зачет | зачет | зачет | хор. | отл. | отл. | хор. | хор. | отл. | хор. | |
181474 | зачет | зачет | зачет | зачет | зачет | зачет | отл. | хор. | хор. | хор. | хор. | хор. | хор. | |
181476 | зачет | зачет | зачет | зачет | зачет | зачет | отл.![]() | отл. | хор. | хор. | удовл. | удовл. | удовл. | |
181477 | зачет | зачет | зачет | зачет | зачет | зачет | отл. | отл. | отл. | отл. | хор. | отл. | хор. | |
181478 | зачет | зачет | зачет | зачет | зачет | зачет | отл. | отл. | отл. | удовл. | удовл. | хор. | удовл. | |
181480 | зачет | зачет | зачет | зачет | зачет | зачет | отл. | отл. | хор. | отл. | хор. | хор. | хор. | |
181483 | зачет | зачет | зачет | незач. | зачет | зачет | хор. | удовл. | удовл. | н/д/к | хор. | удовл. | хор. |
Сведения о текущей аттестации студентов
Курс 3, Механико-машиностроительный факультет, группа МНМ-18, весенний семестр 2020/2021 учебного года
* — дисциплина по выбору или факультативная дисциплина
Номер документа | Коррозия и коррозионностойкие покрытия* | Маркетинг* | Машиностроительные материалы | Методы структурного анализа материалов и контроля качества деталей | Метрология, стандартизация и сертификация | Основы экономики и управления производством | Перенос энергии и массы, основы теплотехники и гидроаэродинамики | Теория и технология термической и химико-термической обработки | Военная подготовка* | Элективные дисциплины по физической культуре и спорту | Физическая культура и спорт | |||||||||||||||||||||||||||||||||
---|---|---|---|---|---|---|---|---|---|---|---|---|---|---|---|---|---|---|---|---|---|---|---|---|---|---|---|---|---|---|---|---|---|---|---|---|---|---|---|---|---|---|---|---|
Ⅱ | Ⅲ | Ⅳ | Ⅴ | Ⅱ | Ⅲ | Ⅳ | Ⅴ | Ⅱ | Ⅲ | Ⅳ | Ⅴ | Ⅱ | Ⅲ | Ⅳ | Ⅴ | Ⅱ | Ⅲ | Ⅳ | Ⅴ | Ⅱ | Ⅲ | Ⅳ | Ⅴ | Ⅱ | Ⅲ | Ⅳ | Ⅴ | Ⅱ | Ⅲ | Ⅳ | Ⅴ | Ⅱ | Ⅲ | Ⅳ | Ⅴ | Ⅱ | Ⅲ | Ⅳ | Ⅴ | Ⅱ | Ⅲ | Ⅳ | Ⅴ | |
181476 | ||||||||||||||||||||||||||||||||||||||||||||
181474 | ||||||||||||||||||||||||||||||||||||||||||||
180671 | ||||||||||||||||||||||||||||||||||||||||||||
180678 | ||||||||||||||||||||||||||||||||||||||||||||
180676 | ||||||||||||||||||||||||||||||||||||||||||||
181480 | ||||||||||||||||||||||||||||||||||||||||||||
180675 | ||||||||||||||||||||||||||||||||||||||||||||
180674 | ||||||||||||||||||||||||||||||||||||||||||||
180684 | ||||||||||||||||||||||||||||||||||||||||||||
180741 | ||||||||||||||||||||||||||||||||||||||||||||
181477 | ||||||||||||||||||||||||||||||||||||||||||||
181478 | ||||||||||||||||||||||||||||||||||||||||||||
180673 | ||||||||||||||||||||||||||||||||||||||||||||
180672 | ||||||||||||||||||||||||||||||||||||||||||||
181483 | ||||||||||||||||||||||||||||||||||||||||||||
180024 |
Посещаемость студентов
Курс 3, Механико-машиностроительный факультет, группа МНМ-18, весенний семестр 2020/2021 учебного года
Номер документа | февраль | март | апрель | май | ||||
---|---|---|---|---|---|---|---|---|
пропуск по уважительной причине | пропуск по неуважительной причине | пропуск по уважительной причине | пропуск по неуважительной причине | пропуск по уважительной причине | пропуск по неуважительной причине | пропуск по уважительной причине | пропуск по неуважительной причине | |
180024 | 0 | 0 | 0 | 0 | 0 | 0 | 0 | 0 |
180671 | 0 | 0 | 0 | 0 | 0 | 0 | 0 | 0 |
180672 | 0 | 0 | 0 | 0 | 0 | 0 | 0 | 0 |
180673 | 0 | 0 | 0 | 0 | 0 | 0 | 0 | 0 |
180674 | 0 | 0 | 0 | 0 | 0 | 0 | 0 | 0 |
180675 | 0 | 0 | 0 | 0 | 0 | 0 | 0 | 0 |
180676 | 0 | 0 | 0 | 0 | 0 | 0 | 0 | 0 |
180678 | 0 | 0 | 0 | 0 | 0 | 0 | 0 | 0 |
180684 | 0 | 0 | 0 | 0 | 0 | 0 | 0 | 0 |
180741 | 0 | 0 | 0 | 0 | 0 | 0 | 0 | 0 |
181474 | 0 | 0 | 0 | 0 | 0 | 0 | 0 | 0 |
181476 | 0 | 0 | 0 | 0 | 0 | 0 | 0 | 0 |
181477 | 0 | 0 | 0 | 0 | 0 | 0 | 0 | 0 |
181478 | 0 | 0 | 0 | 0 | 0 | 0 | 0 | 0 |
181480 | 0 | 0 | 0 | 0 | 0 | 0 | 0 | 0 |
181483 | 0 | 0 | 0 | 0 | 0 | 0 | 0 | 0 |
Кафедра робототехники, мехатроники, динамики и прочности машин
Кафедра робототехники, мехатроники, динамики и прочности машин образована в 2016 году путем слияния кафедры теоретической механики и мехатроники и кафедры динамики и прочности машин им. В.В.Болотина.
Кафедра теоретической механики основана в 1930 году. Научная деятельность сотрудников кафедры охватывает различные области механики (механика абсолютно твёрдого тела, теория упругости и пластичности, теория механизмов и машин, гидромеханика), а также смежные области математики. Многие учёные и преподаватели кафедры получили заслуженную известность своими научными и методическими работами, а сама кафедра выдвинулась в число ведущих кафедр по данному профилю. На базе кафедры проводится курсы повышения квалификации: «Методы аналитической и алгоритмической компенсации систематических погрешностей датчиков инерциальной информации в изменяющихся условиях функционирования» и «Методы навигации и управления движением сети мобильных и стационарных роботов, выполняющих комплексные производственные и технологические задачи».
Кафедра динамики и прочности машин была образована в 1930 году (1930 г. — кафедра Сопротивления материалов, 1969 г. – кафедра Динамики и прочности машин, 2009 г. -2016 г. — кафедра Динамики и прочности машин им. В.В.Болотина). Основная деятельность направлена на подготовку специалистов в области прикладной механики и инженерных методов расчета конструкций на прочность, надежность и безопасность с применением компьютерных технологий. Выпускники кафедры ДПМ работают в областях авиационной и ракетной техники, традиционной и атомной энергетики, промышленного и гражданского строительства, машиностроения, нефтегазового комплекса. На базе кафедры ДПМ создан Центр подготовки и переподготовки (ЦПП) специалистов «Надежность конструкций». С 2005 года ЦПП совместно с ООО «Техсофт» реализует программу повышения квалификации специалистов в области проектирования зданий и сооружений «Применение метода конечных элементов для прочностных расчетов и обеспечения надежности конструкций».
Кафедра РМДиПМ является общеобразовательной, проводит обучение студентов НИУ МЭИ по общетехническим дисциплинам: Сопротивление материалов, Теоретическая механика, Прикладная физика, Прикладная механика, Динамика и прочность машин, Механика материалов и конструкций.
Кафедра РМДиПМ готовит специалистов:
- бакалавр по направлению 15.03.03 Прикладная механика, профиль «Динамика и прочность машин, приборов и аппаратуры». Срок обучения 4 года.
- бакалавр по направлению 15.03.06 Мехатроника и робототехника, профиль “Компьютерные технологии управления в робототехнике и мехатронике» Срок обучения 4 года.
- магистр по направлению 15.04.03 Прикладная механика, программа «Динамика и прочность машин, приборов и аппаратуры». Срок обучения 2 года.
- магистр по направлению 15.04.06 Мехатроника и робототехника, программа: “Разработка компьютерных технологий управления и математического моделирования в робототехнике и мехатронике”. Срок обучения 2 года.
- подготовка кадров высшей квалификации (2 программы аспирантуры) по направлению 01.06.01 Математика и механика, направленности (специальности) 01.
02.01 Теоретическая механика и 01.02.06 Динамика, прочность машин, приборов и аппаратуры. Учебный план и программы дисциплин соответствуют Федеральному государственному образовательному стандарту высшего образования по подготовке кадров высшей квалификации по направлению подготовки 01.06.01 Математика и механика.
Основы управления движением | Конструкция машины
Кратко:
- Металлические ремни прочные. Многослойные металлические ремни прочнее.
- Металл устойчив к царапинам и царапинам, не позволяя бактериям спрятаться и размножаться.
- Металлические ленты не образуют пыли и мусора.
Однослойные металлические ремни прочнее пластмассовых или резиновых ремней. Но им все еще может не хватать прочности и долговечности для работы в приложениях, связанных с поднятием тяжестей и повторяющимися движениями, такими как робототехника.В таких случаях лучше использовать многослойные металлические ремни.
Но являются ли многослойные металлические ремни хорошим выбором для вашей конструкции или применения?
Рассмотрим преимущества и недостатки многослойных металлических ремней по сравнению с их однослойными аналогами и неметаллическими ремнями.
Основные сведения о металлических лентах
Многослойные ленты на конвейерах обладают всеми преимуществами однослойных металлических лент, одновременно повышая прочность и долговечность.
Многослойные ремни похожи на однослойные по конструкции, и оба могут использоваться в бесконечных или открытых конфигурациях.
Бесконечная металлическая лента — это цельный непрерывный металлический лист, сваренный в петлю. Такой ремень долговечен и обеспечивает стабильную, воспроизводимую работу, что делает его полезным для автоматизированной сборки, пищевой промышленности и медицинских устройств.
Приводные ленты похожи на конвейерные ленты, но используются со специальными синхронизирующими шкивами, что делает их полезными для повторяемого и точного движения.
Металлические приводные ленты, с другой стороны, имеют открытую конфигурацию. Они имеют металлическую конструкцию с ремнями, но закреплены на каждом конце.Они обычно используются для чрезвычайно точного и воспроизводимого движения, которое необходимо при создании 3D-принтеров и роботов.
Металлические ремни могут изготавливаться из различных сплавов нержавеющей стали и титана, а также из никелевых сплавов, таких как инконель и инвар. Некоторые из этих материалов устойчивы к низким температурам, другие — к коррозии, а некоторые имеют высокие пределы прочности и текучести. Выбор материала зависит от предполагаемого применения.
Как и их однослойные аналоги, многослойные приводные ленты обеспечивают нулевой люфт, который возникает в результате слишком большого зазора между отверстиями ремня ГРМ и штифтом синхронизирующего шкива.Как правило, требуется некоторый зазор, чтобы избежать столкновения и позволить штифтам войти в отверстия, но это может вызвать люфт при переворачивании ремня.
Когда шкив поворачивается, чтобы переместить ремень назад, штифты должны сначала переместиться с одной стороны своих отверстий на другую, прежде чем толкать ремень. Этот небольшой люфт может привести к неточности позиционирования в профиле движения. Для устранения этого могут быть разработаны прецизионные металлические ремни.
Металлические ремни работают со шкивами без зубцов или канавок, что снижает точность и повреждения от люфта.
Различия в многослойных ремнях
Многослойные ремни состоят из 2-7 уложенных друг на друга лент толщиной от 0,003 до 0,005 дюйма. Это сводит к минимуму общее напряжение, прикладываемое к ремню, и позволяет ремню выдерживать большую растягивающую нагрузку через увеличенное поперечное сечение -секционная площадь. Дополнительная прочность также продлевает срок службы ремней.
Многослойная конструкция также добавляет жесткости, что увеличивает его модуль упругости, так что ремень может противостоять люфту из-за любых оставшихся зазоров между отверстиями ГРМ и штифтами, которые невозможно спроектировать. Это может быть полезно во многих приложениях. Например, у некоторых роботов-манипуляторов есть два стальных ремня, работающих в тандеме, причем один ремень обеспечивает реверсивное движение. Благодаря неэластичности стального ремня эта конструкция может выдерживать быстрое ускорение и движение задним ходом, не вызывая люфта. Многослойные ремни обычно используются таким образом, чтобы выдерживать высокие нагрузки и ускорения.
Изготовление многослойных ремней сложнее из-за того, что все слои должны быть точно изготовлены, а затем свариваться вместе на концевом выступе ремня.Каждый поясной слой имеет немного разную длину и должен быть прикреплен так, чтобы он мог подходить к другим слоям при намотке на шкив. Концевой язычок — еще один ключевой элемент для обеспечения длительного срока службы ремня, поскольку он подвергается высоким нагрузкам. Из-за этого дизайн вкладки так же важен, как и качественная прецизионная сварка, использованная для ее создания.
Непористые поверхности лент из нержавеющей стали устойчивы к повреждениям, что делает их менее уязвимыми для бактерий или микробов в следах и царапинах.
Многослойные ремни обладают множеством преимуществ, включая их прочность и гибкость, но у них есть несколько других.
Толщина ремня и размер шкива определяют срок службы ремня. Шкив большего размера обычно означает, что ремень может выдерживать большую нагрузку. Но многослойные ремни могут выдерживать большую нагрузку без увеличения диаметра шкива. Несколько уровней обеспечивают прочность более толстой ленты, но работают вместе, чтобы получить гибкость меньшей ленты. Приложения, в которых полностью используются преимущества многослойных металлических ремней, включают перемещение тяжелых грузов без места для шкива подходящего размера, необходимого для однослойного, но более толстого ремня.Эта конструкция может работать с шкивами диаметром от 1,5 дюйма.
Как указывалось ранее, производство многослойных металлических ремней сложнее, что приводит к более высокой начальной стоимости. Это изначально недостаток, но эти ремни более рентабельны в течение всего срока службы из-за их повышенной прочности.
По сравнению с традиционными ремнями без питания, более длительный срок службы многослойных металлических ремней и меньшие требования к очистке и техническому обслуживанию помогают компенсировать первоначальные затраты и делают их лучшим вариантом в долгосрочной перспективе.
Металлические ремни могут деформироваться и не подлежат ремонту при неправильном использовании или сильных ударах. Защита металлических лент, одно- или многослойных, от повреждений такого типа является ключом к обеспечению длительного срока службы ремня.
Многослойные металлические ремни в действии
Фирма пыталась получить апробированные и коммерциализированные новые технологии для робототехники. Проекты включали новые способы подъема и поворота тяжелых грузов в области складирования, логистики, медицины и пищевой промышленности.
Фирма работала над одной машиной, на которой использовалась однослойная металлическая лента, изготовленная из металла местного производства. Ремень имел ширину 6 мм и толщину 0,2 мм, но он выходил из строя, когда крутящий момент на ремне превышал 25 Нм. Затем клиент работал с командой инженеров Belt Technologies.
Одна из проблем заключалась в том, что они не могли изменить диаметр шкива. Итак, команда разработала и изготовила ленту из нержавеющей стали с шестью слоями, каждый толщиной 0,125 мм. Это позволяет машине выдерживать требуемый крутящий момент 150 Нм без увеличения напряжения изгиба.Следовательно, общие нагрузки на ремень уменьшаются, что увеличивает срок его службы.
Фирма увидела успех прототипа ремня, который в основном использовалась для демонстрации, и заказала версии новых металлических ремней с немного измененной длиной для использования в устройствах здравоохранения.
Говоря о приложениях в сфере здравоохранения, металлические ремни позволяют производителям медицинского оборудования соблюдать правила безопасности для конвейерных лент с приводом от двигателя в фармацевтических и медицинских приложениях. Металлические ремни, в отличие от пластиковых или резиновых версий, противостоят бактериям, которые могут повредить фармацевтические препараты. Они также более гигиеничны в силу того, что их легче чистить и они устойчивы к воздействию воды и моющих средств.
Многослойные металлические ленты, занявшие нишу в робототехнике. Металлические приводные ленты открытой конфигурации, тип многослойной ленты, могут выполнять многие задачи с практически нулевым люфтом, в том числе:
- Позиционирующие каретки
- Роботизированные манипуляторы
- Изготовление ЖК-дисплеев
- Приводы оптических элементов
Они Правильно для вас?
Помимо большей прочности и гибкости, чем однослойные ремни, многослойные ремни обладают всеми характеристиками и преимуществами других цельнометаллических ремней, в том числе:
- Высокое соотношение прочности и веса
- Долговечность и более длинный ремень срок службы по сравнению с альтернативами
- Жесткий (не растягивающийся) для повышения точности
- Устойчивость к колебаниям температур
- Устойчивость к коррозии, ржавчине и перегреву
Многослойные ленты на конвейерах обеспечивают все преимущества однослойных металлических лент, одновременно добавляя дополнительную прочность и долговечность.
Кроме того, они:
- Не требуют смазки
- Соответствуют самым строгим требованиям USDA для пищевой промышленности
- Обеспечивают высокую точность и повторяемость
- Непористые и устойчивы к повреждению поверхности
- Широкие возможности настройки для различных отраслей промышленности и приложения
- Не образуют такие частицы, как HTD или плоские неопреновые ленты, что делает их хорошо подходящими для чистых помещений.
Денис Ганьон — генеральный директор, а Алан Воски — президент Belt Technologies Inc.в Агаваме, Массачусетс. Свяжитесь с ними здесь.
Основы автоматизации машин | Library.Automationdirect.com
Системы автоматизации должны объединять несколько подсистем и компонентов питания и управления в единое целое. Прочтите, чтобы узнать больше об основах автоматизации машин.
Чип МакДэниел, который занимается техническим маркетингом в AutomationDirect, написал статью для выпуска журнала InTech за март / апрель 2019 года под названием «Основы машинной автоматизации». В статье он сначала излагает доводы в пользу улучшения систем автоматизации.
Столкнувшись с постоянно растущим давлением затрат и требований по повышению производительности, машиностроители активно ищут новые Решения по автоматизации с улучшенным соотношением цена / производительность. В ответ на эти требования, поставщики часто должны включать коммерческие готовые компоненты и другие технологии для обеспечения большей производительности при меньших затратах в меньшие форм-факторы.
Статья тогда переходит к обсуждению основных элементов, обычно используемых в системах автоматизации.
Компоненты и подсистемыАвтоматизация станка Система в основном состоит из компонентов питания и управления. Для меньшего машина, они могут быть размещены на одной панели; тогда как для больших машин может потребоваться несколько панелей, часто одна для управления, а другая для питания. Основные подсистемы и компоненты системы автоматизации станка:
- распределение питания
- управление двигателем и приводы
- система безопасности
- программируемые контроллеры
- дискретный и аналоговый ввод / вывод
- системы связи
- человеко-машинный интерфейс (HMI)
для небольших машин, одна панель часто используется для размещения как системы распределения энергии, так и компонентов управления.
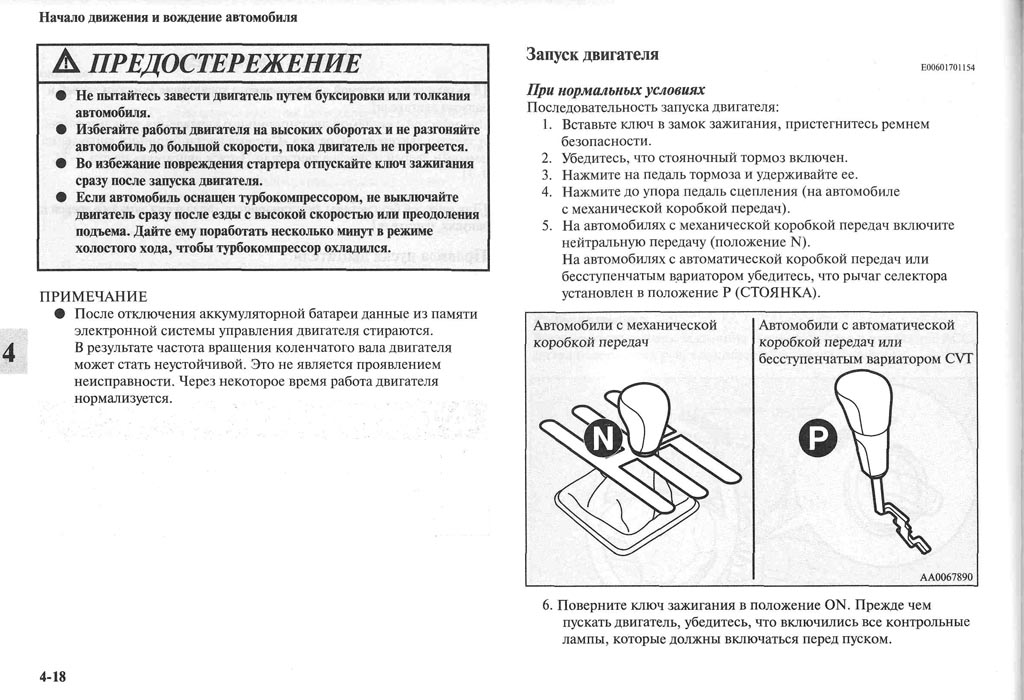
Для машины меньшего размера, одна панель часто используется для размещения силовых Система распределения и элементы управления .
Распределение энергииНа машине NFPA 79: Электрический стандарт для промышленного оборудования является эталоном для обеспечения безопасности промышленных машин, связанных с опасностями пожара и поражения электрическим током. Некоторые из основные требования к распределению мощности управления машиной, обсуждаемые в эти стандарты включают использование надлежащих средств отключения, защиту персонала от контакта с электрическими опасностями и защиты оборудования от перегрузки по току и перегрузки.
Управление двигателем и приводы Двигатели имеют специальные
потребности в управлении машиной. Для каждого двигателя правильная форма электрического управления
требуется, от простого включения / выключения до более сложных приложений с регулируемой скоростью. Устройства управления двигателем включают ручные пускатели двигателя, контакторы двигателя и
пускатели с перегрузками, приводы и устройства плавного пуска.
Эти ручные пускатели двигателей и контакторы Fuji от AutomationDirect обладают высокой коммутационной способностью и объединяют функции автоматического выключателя в литом корпусе и теплового реле перегрузки.
Цепь двигателя должна включают как защиту от перегрузки по току (короткое замыкание), так и защиту от перегрузки. Этот обычно состоит из защиты параллельной цепи, такой как предохранители надлежащего номинала, и пускатель двигателя с устройствами защиты от перегрузки, такими как тепловые перегрузки, но может потребоваться дополнительная защита.
Дополнительная защита машины Компоненты управления включают потерю охлаждения и аномальные температуры. Земля Также необходима защита от короткого замыкания, поэтому важно правильное заземление.
Системы безопасности Оценка риска
управляет конструкцией системы безопасности по мере необходимости для удаления энергии, вызывающей движение,
включая электрическую и гидравлическую энергию, чтобы безопасно останавливать оборудование на
защита персонала и машин. Существуют различные методы
внедрение систем безопасности.
В приложениях для управления небольшими машинами реле безопасности, вероятно, самый простой способ интегрировать функции безопасности для аварийный останов, наблюдение за защитной дверью или защита оператора, достигающего через световую завесу.В более совершенных машинах контроллеры с повышенным уровнем безопасности предоставляют те же функции, но могут упростить интеграцию нескольких систем безопасности устройства .
Программируемые контроллеры и ввод / выводДоступен в форме факторы от малого до большого, контроллер машины может быть программируемой логикой контроллер (PLC), программируемый контроллер автоматизации (PAC) или ПК.
Программное обеспечение, используемое для Программирование семейства контроллеров следует внимательно изучить на предмет простоты использования и Другие свойства.
Использование той же программной платформы для программирования
Семейство контроллеров становится нормой. Это позволяет дизайнеру сначала
запрограммируйте систему, а затем выберите правильный контроллер в зависимости от его возможностей
для обработки необходимого количества точек ввода / вывода, а также специальных функций, таких как
пропорциональное, интегральное, производное управление и обработка данных.
Дискретный и аналоговый входы и выходы соединяют контроллер с датчиками и исполнительными механизмами машины. Эти сигналы могут исходить от главной панели управления через клеммную колодку. с подключением к полевым устройствам, но архитектура распределенного ввода / вывода часто лучшее решение.
Коммуникационные системыДругая важная часть управления машинами сейчас и в будущем — это обширная коммуникация возможности. Рекомендуется иметь несколько портов Ethernet и последовательных портов. доступны для интеграции в различное оборудование, компьютеры, HMI и бизнес и корпоративные системы.
В дополнение к нескольким коммуникационным портам на этом контроллере BRX, дополнительные порты добавляются с помощью коммутатора STRIDE Industrial Ethernet и адаптера последовательного интерфейса GS привода в Ethernet.
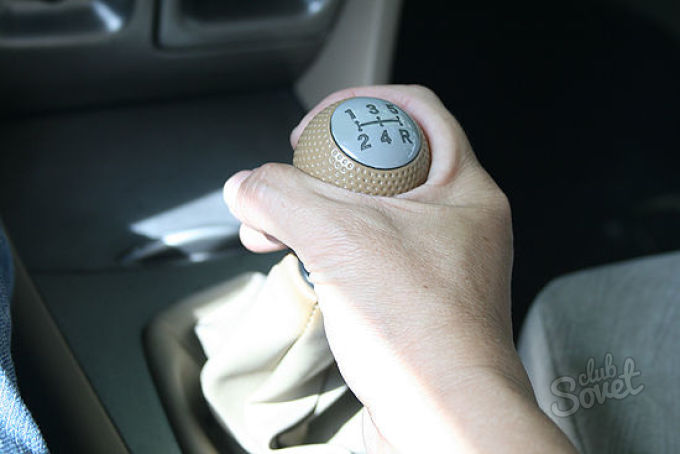
Несколько высокоскоростных Порты Ethernet обеспечивают оперативную связь HMI, а также одноранговую и сеть бизнес-систем. Поддержка промышленных протоколов Ethernet, в том числе EtherNet / IP и Modbus TCP / IP также важны для сканера / клиента и подключения адаптера / сервера.
Человеко-машинный интерфейсHMI показывает важную информацию о состоянии машины с использованием графического и текстового представлений. ЧМИ могут быть в в виде сенсорных панелей, текстовых панелей, дисплеев сообщений или промышленных мониторов.Они используются для мониторинга, контроля, отчетов о состоянии и многих других функции.
Системы автоматизации машин состоят из нескольких
подсистемы и компоненты для обеспечения необходимого распределения мощности, безопасности,
и контроль в реальном времени. Каждая из этих подсистем и компонентов должна работать
вместе, и многие из них часто связаны друг с другом посредством проводки или
все чаще через цифровые каналы связи.
Тщательный дизайн и предварительное планирование обеспечат надежность, простоту обслуживания и гибкость системы автоматизации.
Чтобы прочитать другие статьи по теме, щелкните здесь.
Первоначально опубликовано: апрель 2019 г.
Система управления | технология | Британника
Система управления , означает, что переменное количество или набор переменных величин приводится в соответствие с предписанной нормой. Он либо сохраняет значения контролируемых величин постоянными, либо заставляет их изменяться заданным образом. Система управления может приводиться в действие электричеством, механическими средствами, давлением текучей среды (жидкости или газа) или комбинацией средств.Когда в цепи управления задействован компьютер, обычно удобнее управлять всеми системами управления электрически, хотя довольно часто встречаются смеси.
Разработка систем управления.
Системы управления тесно связаны с концепцией автоматизации ( q. v. ), но два основных типа систем управления, с прямой связью и обратной связью, имеют классическое происхождение. Ткацкий станок, изобретенный Жозефом Жаккаром из Франции в 1801 году, является ранним примером прямой связи; набор перфокарт, запрограммированных на ткацкие станки; никакая информация из процесса не использовалась для исправления работы машины.Подобное упреждающее управление было включено в ряд станков, изобретенных в 19 веке, в которых режущий инструмент повторял форму модели.
Управление с обратной связью, в котором информация из процесса используется для корректировки работы машины, имеет еще более давнюю историю. Римские инженеры поддерживали уровень воды в своей системе акведуков с помощью плавающих клапанов, которые открывались и закрывались на соответствующих уровнях. Голландская ветряная мельница 17 века удерживалась лицом к ветру за счет действия вспомогательной лопасти, которая перемещала всю верхнюю часть мельницы.Самый известный пример промышленной революции — это управляющий шаровой шарнир Джеймса Ватта 1769 года, устройство, которое регулировало поток пара в паровой двигатель для поддержания постоянной скорости двигателя, несмотря на изменяющуюся нагрузку.
Первый теоретический анализ системы управления, который представил модель регулятора Ватта на основе дифференциального уравнения, был опубликован Джеймсом Клерком Максвеллом, шотландским физиком, в 19 веке. Вскоре работа Максвелла была обобщена, и теория управления была развита на основе ряда статей, включая заметное исследование системы автоматического рулевого управления U.Линкор S. «Нью-Мексико», опубликованный в 1922 году. В 1930-х годах была разработана электрическая обратная связь в телефонных усилителях для дальней связи и общая теория сервомеханизма, с помощью которой небольшое количество энергии управляет очень большим количеством и автоматически производит исправления. Затем последовали пневматический контроллер, лежащий в основе разработки первых автоматизированных систем в химической и нефтяной промышленности, и аналоговый компьютер. Все эти разработки легли в основу разработки теории систем управления и приложений во время Второй мировой войны, таких как зенитные батареи и системы управления огнем.
Большинство теоретических исследований, а также практических систем до Второй мировой войны были однопетлевыми — то есть они включали просто обратную связь из одной точки и корректировку из одной точки. В 1950-е годы исследовались возможности многоконтурных систем. В этих системах обратная связь может быть инициирована более чем в одной точке процесса, а исправления могут быть сделаны более чем в одной точке.Внедрение аналогового и цифрового вычислительного оборудования открыло путь для гораздо большей сложности теории автоматического управления, шаг вперед, получивший название «современное управление», чтобы отличить его от более старого, более простого «классического управления».
Основные принципы.
За немногими и относительно незначительными исключениями, все современные системы управления имеют две общие характеристики. Их можно описать следующим образом: (1) Величина контролируемой величины изменяется двигателем (это слово используется в обобщенном смысле), который получает энергию от локального источника, а не от входящего сигнала. Таким образом, имеется большое количество энергии для осуществления необходимых изменений контролируемой величины и для гарантии того, что операции изменения регулируемой величины не загружают и не искажают сигналы, от которых зависит точность управления. (2) Скорость, с которой энергия подается в двигатель для изменения значения контролируемой величины, определяется более или менее напрямую некоторой функцией разницы между фактическим и желаемым значениями регулируемой величины.Таким образом, например, в случае термостатической системы нагрева подача топлива в печь определяется тем, выше или ниже фактическая температура, чем заданная температура. Система управления, обладающая этими фундаментальными характеристиками, называется системой управления с обратной связью или сервомеханизмом (см. Рисунок). Системы управления с обратной связью — это системы с прямой связью.
Основные компоненты типичной системы управления с обратной связью
Encyclopædia Britannica, Inc.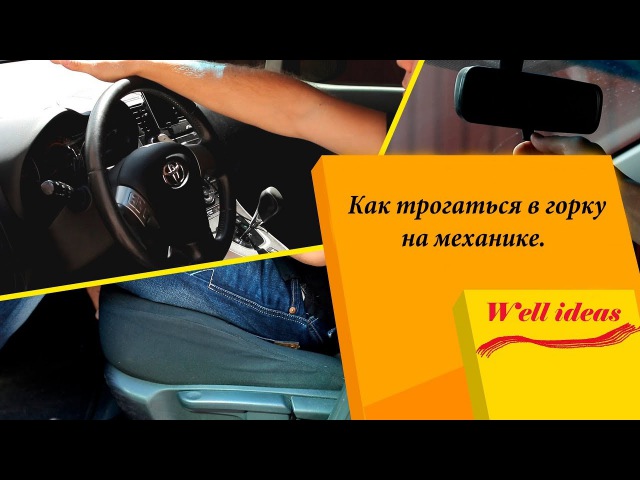
Стабильность системы управления в значительной степени определяется ее реакцией на внезапно приложенный сигнал или переходный процесс. Если такой сигнал заставляет систему чрезмерно исправлять себя, может возникнуть явление, называемое перехватом, при котором система сначала чрезмерно корректирует себя в одном направлении, а затем чрезмерно корректирует себя в противоположном направлении. Поскольку охота нежелательна, обычно принимаются меры по ее исправлению. Самая распространенная корректирующая мера — это добавление демпфирования где-нибудь в системе.Демпфирование замедляет реакцию системы и позволяет избежать чрезмерных выбросов или корректировок. Демпфирование может проявляться в виде электрического сопротивления в электронной схеме, применения тормоза в механической цепи или нагнетания масла через небольшое отверстие, как при демпфировании амортизатора.
Другой метод проверки устойчивости системы управления — определить ее частотную характеристику — то есть ее реакцию на непрерывно изменяющийся входной сигнал на различных частотах. Затем выходной сигнал системы управления сравнивается с входом по амплитуде и фазе — i.е., степень рассогласования входных и выходных сигналов. Частотная характеристика может быть определена экспериментально, особенно в электрических системах, или рассчитана математически, если постоянные системы известны. Математические вычисления особенно полезны для систем, которые могут быть описаны обыкновенными линейными дифференциальными уравнениями. Графические ярлыки также очень помогают в изучении реакции системы.
При разработке современных систем управления используются и другие методы.Адаптивное управление — это способность системы изменять свои собственные операции для достижения наилучшего режима работы. Общее определение адаптивного управления подразумевает, что адаптивная система должна быть способна выполнять следующие функции: предоставление непрерывной информации о текущем состоянии системы или идентификация процесса; сравнение текущей производительности системы с желаемой или оптимальной производительностью и принятие решения об изменении системы для достижения определенной оптимальной производительности; и инициирование надлежащей модификации, чтобы довести систему управления до оптимума. Эти три принципа — идентификация, решение и модификация — присущи любой адаптивной системе.
Управление с динамической оптимизацией требует, чтобы система управления работала таким образом, чтобы удовлетворялся определенный критерий производительности. Этот критерий обычно формулируется таким образом, что управляемая система должна переместиться из исходного положения в новое за минимально возможное время или с минимальными общими затратами.
Управление обучением подразумевает, что система управления обладает достаточными вычислительными возможностями, так что она может создавать представления математической модели управляемой системы и изменять свои собственные операции, чтобы воспользоваться преимуществами этих недавно разработанных знаний.Таким образом, обучающаяся система управления является дальнейшим развитием адаптивного контроллера.
Управление с несколькими переменными без взаимодействия включает большие системы, в которых размер внутренних переменных зависит от значений других связанных переменных процесса. Таким образом, однопетлевых методов классической теории управления будет недостаточно. Для разработки соответствующих систем управления такими процессами необходимо использовать более сложные методы.
автоматизация | Технология, типы, рост, история и примеры
Автоматизация , применение машин к задачам, которые когда-то выполнялись людьми, или, все чаще, к задачам, которые иначе были бы невозможны.Хотя термин «механизация» часто используется для обозначения простой замены человеческого труда машинами, автоматизация обычно подразумевает интеграцию машин в самоуправляемую систему. Автоматизация произвела революцию в тех областях, в которых она была внедрена, и едва ли есть какой-либо аспект современной жизни, на который она не повлияла.
Британская викторина
Гаджеты и технологии: факт или вымысел?
Виртуальная реальность используется только в игрушках? Использовались ли когда-нибудь роботы в бою? В этой викторине вы узнаете о гаджетах и технологиях — от компьютерных клавиатур до флэш-памяти.
Термин «автоматизация» появился в автомобильной промышленности примерно в 1946 году для описания все более широкого использования автоматических устройств и средств управления на механизированных производственных линиях. Происхождение этого слова приписывается Д.С. Хардеру, в то время руководителю инженерного отдела Ford Motor Company. Этот термин широко используется в производственном контексте, но он также применяется за пределами производства в связи с множеством систем, в которых происходит значительная замена человеческих усилий и интеллекта механическими, электрическими или компьютеризированными действиями.
В общем случае автоматизация может быть определена как технология, связанная с выполнением процесса с помощью запрограммированных команд в сочетании с автоматическим управлением с обратной связью для обеспечения надлежащего выполнения инструкций. Полученная система способна работать без вмешательства человека. Развитие этой технологии все больше зависит от использования компьютеров и компьютерных технологий. Следовательно, автоматизированные системы становятся все более изощренными и сложными.Продвинутые системы представляют собой уровень возможностей и производительности, который во многих отношениях превосходит способности людей выполнять те же действия.
Технология автоматизации достигла такой степени, что на ее основе развился ряд других технологий, получивших признание и собственный статус. Робототехника — одна из таких технологий; это специализированная отрасль автоматизации, в которой автоматизированная машина обладает определенными антропоморфными или человекоподобными характеристиками.Наиболее типичная человеческая характеристика современного промышленного робота — это его механическая рука с приводом. Рука робота может быть запрограммирована на выполнение последовательности движений для выполнения полезных задач, таких как загрузка и разгрузка деталей на производственной машине или выполнение последовательности точечной сварки на деталях из листового металла кузова автомобиля во время сборки. Как видно из этих примеров, промышленные роботы обычно используются для замены рабочих на фабриках.
В этой статье рассматриваются основы автоматизации, в том числе ее историческое развитие, принципы и теория работы, приложения на производстве и в некоторых сферах услуг и отраслей, важных в повседневной жизни, а также влияние на человека и общество в целом. В статье также рассматривается развитие и технология робототехники как важная тема автоматизации. По связанным темам см. Информатика и обработка информации.
Историческое развитие автоматизации
Технология автоматизации эволюционировала из смежной области механизации, которая зародилась в период промышленной революции.Механизация относится к замене силы человека (или животного) механической силой той или иной формы. Движущей силой механизации была склонность человечества создавать инструменты и механические устройства. Здесь описаны некоторые важные исторические достижения в области механизации и автоматизации, ведущие к современным автоматизированным системам.
Ранние разработки
Первые орудия из камня отражали попытки доисторического человека направить свою физическую силу под контроль человеческого разума.Несомненно, тысячи лет потребовались для разработки простых механических устройств и машин, таких как колесо, рычаг и шкив, с помощью которых можно было увеличить силу человеческих мышц. Следующим шагом была разработка механических машин, для работы которых не требовалась человеческая сила. Примеры этих машин включают водяные колеса, ветряные мельницы и простые паровые устройства. Более 2000 лет назад китайцы разработали трип-молоты, приводимые в движение проточной водой и водяными колесами.Ранние греки экспериментировали с простыми реактивными двигателями, работающими от пара. Механические часы, представляющие собой довольно сложную сборку с собственным встроенным источником питания (гирькой), были разработаны около 1335 года в Европе. Ветряные мельницы с механизмами автоматического поворота парусов были разработаны в средние века в Европе и на Ближнем Востоке. Паровая машина стала крупным достижением в развитии механических машин и положила начало промышленной революции. За два столетия, прошедшие с момента появления парового двигателя Ватта, были разработаны двигатели и механизмы, которые получают энергию из пара, электричества, химических, механических и ядерных источников.
Каждая новая разработка в истории механических машин привносила повышенные требования к устройствам управления, чтобы использовать мощность машины. Самые ранние паровые машины требовали, чтобы человек открывал и закрывал клапаны, сначала для впуска пара в поршневую камеру, а затем для его выпуска. Позже был разработан золотниковый механизм для автоматического выполнения этих функций. Тогда единственной потребностью человека-оператора было регулирование количества пара, регулирующего скорость и мощность двигателя.Это требование к человеческому вниманию при работе парового двигателя было устранено регулятором с летающим шаром. Это устройство, изобретенное Джеймсом Ваттом в Англии, состояло из утяжеленного шара на шарнирном рычаге, механически соединенного с выходным валом двигателя. Когда скорость вращения вала увеличивалась, центробежная сила заставляла утяжеленный шар перемещаться наружу. Это движение управляло клапаном, который уменьшал количество пара, подаваемого в двигатель, тем самым замедляя двигатель. Регулятор с летающим мячом остается элегантным ранним примером системы управления с отрицательной обратной связью, в которой увеличивающийся выход системы используется для уменьшения активности системы.
Отрицательная обратная связь широко используется как средство автоматического управления для достижения постоянного рабочего уровня системы. Типичным примером системы управления с обратной связью является термостат, используемый в современных зданиях для регулирования температуры в помещении. В этом устройстве снижение температуры в помещении вызывает замыкание электрического переключателя, таким образом, включается нагревательный элемент. При повышении температуры в помещении переключатель размыкается и подача тепла отключается. Термостат можно настроить на включение нагревательного элемента при любой конкретной уставке.
Еще одним важным достижением в истории автоматизации стал жаккардовый ткацкий станок (см. Фотографию), который продемонстрировал концепцию программируемого станка. Около 1801 года французский изобретатель Жозеф-Мари Жаккар изобрел автоматический ткацкий станок, способный создавать сложные узоры на текстиле, управляя движениями множества челноков из нитей разного цвета. Выбор различных рисунков определялся программой, содержащейся в стальных картах, в которых были пробиты отверстия. Эти карты были предками бумажных карт и лент, которые управляют современными автоматами.Концепция программирования машины получила дальнейшее развитие в конце XIX века, когда Чарльз Бэббидж, английский математик, предложил сложную механическую «аналитическую машину», которая могла бы выполнять арифметические операции и обработку данных. Хотя Бэббидж так и не смог его завершить, это устройство было предшественником современного цифрового компьютера. См. Компьютеры.
Жаккардовый ткацкий станок, гравюра, 1874 г. В верхней части машины находится стопка перфокарт, которые будут подаваться в ткацкий станок для управления ткацким рисунком.Этот метод автоматической выдачи машинных инструкций использовался компьютерами еще в 20 веке.
The Bettmann ArchiveОсновы контроля качества
Градация рабочего места является важным элементом при подготовке земли к застройке. Несмотря на то, что это может быть дорогостоящий процесс, сортировка играет решающую роль в составлении карты обзора развития строительной площадки.
Сегодня появились машинные технологии для упрощения процесса сортировки и устранения неэффективности.Контроль качества быстро внедряется на стройплощадках по всей стране, а рентабельность инвестиций в технологию контроля уклона может повысить прибыль подрядчика. Соединение системы контроля уклона с гусеничным бульдозером или автогрейдером — отличный способ получить огромную окупаемость инвестиций. Система контроля оценок дает подрядчикам точность, необходимую для того, чтобы предлагать более конкурентоспособные предложения и, в свою очередь, получать больше рабочих мест.
При использовании системы контроля содержания окупаемость инвестиций практически мгновенно окупается.Например, девелопер планирует построить на участке земли торговый центр с огромной парковкой, коммунальным хозяйством и прудом. Во-первых, разработчик наймет инженера, который построит двухмерное представление трехмерной поверхности земли или топора. На основе этой карты создается дизайн торгового центра.
Когда проект готов, подрядчики привлекаются для подготовки сметы. Используя систему управления классами, подрядчики могут нанести на объект саму топографию, чтобы проверить количество инженеров на исходной трехмерной контурной карте существующего объекта. Этот процесс известен как взлет, при котором плановое количество сравнивается с взлетным с помощью программного обеспечения для строительства. После завершения своей точной сметы подрядчик может создать конкурентное предложение и выиграть контракт.
Затем подрядчик создает трехмерную модель из цифрового проекта, а затем локализует ее и интегрирует модель в локальный сборщик данных и машину для контроля качества. Когда система готова к работе, точность подрядчика повышается, что сокращает количество проходов для успешного завершения работы.Контроль уклона радикально устраняет необходимость в стойках уклона и дополнительных рабочих на строительной площадке даже во время процесса проверки.
Системы контроля качества
Сегодня на рынке доступно множество систем контроля качества:
- Двухмерные системы начального уровня — Двухмерная система контроля уклона позволяет операторам настраивать лазерный передатчик для резки до желаемого уклона как на плоских, так и на наклонных поверхностях.
Двухмерная система использует датчики угла и вращения для расчета поперечного наклона каждой стороны отвала, а также лазерный приемник для контроля высоты. Используя автогрейдер или гусеничный бульдозер, система позволяет отслеживать линию, предыдущий проход, бордюр и желоб. С помощью лазерных приемников операторы могут использовать систему для точной профилирования плоских поверхностей. Двухмерная система контроля уклона идеально подходит для применений с жесткими допусками и готовой работы с уклоном. Часто эти системы поставляются с блоком управления, который включает в себя программное обеспечение с широким набором функций, специально разработанное для управления подъемом и / или наклоном бульдозеров и автогрейдеров.
- Трехмерные системы — С трехмерной системой управления уклоном расчетные высоты задания вводятся в блок управления гусеничного бульдозера или автогрейдера. Приемник на машине считывает сигналы GPS, принятые поднятой антенной, а также корректирующие данные, передаваемые станцией на рабочем месте, чтобы вычислить точное и современное положение.
Компьютер блока управления сравнивает положение переднего края с проектными отметками и затем отображает информацию о выемках и насыпях. Трехмерная система лучше всего подходит для сложных контуров.Автоматические системы как для 2-х, так и для 3-х измерений даже регулируют лезвие для оператора. Оба метода позволяют достичь точной высоты и угла при использовании точного количества материалов и рабочей силы для выполнения работы.
- Роботизированные тахеометры — Роботизированные тахеометры удобны, когда доступ к небу ограничен, например, при выполнении работ внутри здания или туннеля. Это датчики трехмерного позиционирования для трехмерной системы управления уклоном. Датчик представляет собой электромеханическое и оптическое устройство позиционирования.Работает везде, где есть препятствия для обзора неба. Кроме того, это один из самых точных датчиков позиционирования, доступных для приложений трехмерного контроля уклона.
- Миллиметровая система GPS —MMGPS сочетает в себе преимущества лазера и GPS в одной универсальной и простой в использовании системе.
Эта технология может повысить точность сортировки до 300 процентов по сравнению с большинством систем трехмерных машин. Передатчик MMGPS излучает световую стену высотой 33 фута и диаметром до 1000 футов, а с датчиком управления машиной, добавленным к существующей системе GPS, вертикальная точность значительно повышается.
Grade Control WorkFlow
Теперь вы выбрали систему контроля уклонов, которая наилучшим образом соответствует потребностям вашей рабочей площадки. Когда вы будете готовы приступить к проекту, очень важно правильно реализовать контроль качества, чтобы ваши инвестиции окупились. Поскольку подрядчики сокращают свои операционные расходы с помощью этой технологии, контроль содержания оказывает на них значительное влияние на протяжении всего рабочего цикла. Чтобы обеспечить эффективную окупаемость инвестиций, подрядчикам важно выполнять безупречный рабочий процесс контроля уклонов — пошаговый процесс, помогающий им выполнять работы и максимизировать рентабельность инвестиций при использовании технологии контроля уклонов. Пройдите через день из жизни подрядчика с использованием контроля уклона:
- Setup / Topo — Инженер устанавливает четыре контрольные точки для конкретной рабочей площадки с помощью определенных измерений. Инженер измерит контрольные точки с помощью вездехода, чтобы установить всю рабочую площадку. Затем инженер создаст топо рабочей площадки. Где бы ни происходила разработка объекта, инженер покрывает всю рабочую площадку, чтобы обеспечить регистрацию всех измерений. Топографическая карта будет отображать все изменения высот на площадке, и инженер создаст проект площадки после того, как все измерения будут обеспечены и выполнены.
- Проект —Проект строительной площадки определяет расположение всех построек, включая подземные коммуникации, парковки и все остальное, что землевладелец хочет построить на участке.
- Takeoff / Estimate —В части рабочего процесса контроля содержания на этапе взлета / оценки подрядчики, составляющие заявки, будут сравнивать то, что инженер-конструктор предоставил для количеств на объекте.
Затем подрядчики будут проверять коммунальные услуги. Подрядчики также подтвердят материалы, которые потребуются для перемещения, с помощью системы управления классами.Затем они сравнят поверхности, чтобы убедиться, что вся информация инженера точна, и можно начинать строительство на основе измерений инженера. F0 + 90 (футы и десятые доли фута) измеряются на карте, чтобы нарисовать картину для подрядчиков, сообщая им расстояние выемки и насыпи. Это помогает подрядчикам спланировать оборудование, которое будет наиболее эффективно перемещать материал, позволяя им иметь самые низкие затраты на ярд.
- Выигрыш тендера —Без контроля содержания проект будет дороже и сложнее дать оценку с низкой стоимостью.В некоторых случаях контроль уклона позволяет строительной бригаде использовать один гусеничный бульдозер вместо двух. Кроме того, подрядчику-победителю не нужно нанимать стороннего геодезиста на протяжении всего проекта, так как технология обеспечит поддержку команды.
- Модель —После того, как тендерное предложение будет выиграно и строительство будет готово к началу, трехмерная модель с использованием программного обеспечения позволит подрядчикам строить выемки, карты насыпи и форматировать проект для работы на специальном программном обеспечении для контроля содержания.
Затем для оценки используется трехмерная модель.
- Локализация из проекта —На данном этапе рабочего процесса подрядчик измеряет контрольные точки, чтобы ориентироваться на площадке. Затем он / она выполнит измерения местных координат север-восток-возвышение, привязав их к широте, долготе и высоте эллипсоида.
- Импорт трехмерной модели в бульдозер на гусеничном ходу — Используя простой USB-порт, подрядчик может загрузить координаты поверхности в машину. С помощью вашего дилера специалист по контролю качества может поддерживать подрядчика на протяжении всего процесса.
- Поддержка — Местный дилер сопровождает подрядчика на каждом этапе его пути, чтобы гарантировать эффективность контроля качества и достижение результатов для увеличения чистой прибыли подрядчика. У дилеров есть запасные части на полках для обеспечения бесперебойной работы, а у специализированных специалистов — для бесперебойной работы.
Контроль оценок по сравнению с отсутствием
Чтобы лучше представить преимущества использования контроля уклона, рассмотрим проект на строительной площадке с 100 000 кубических ярдов материала для перемещения и 50 000 квадратных ярдов парковки.
- Мобилизация —Мобилизация рабочей площадки для разработки без контроля уклона требует двух самосвалов с шарнирно-сочлененной рамой, одного экскаватора, двух бульдозеров и одного трактора. При почасовой ставке 120 долларов мобилизация сайта обойдется примерно в 2160 долларов. При контроле уклона подрядчикам по-прежнему нужны два ADT, один экскаватор и один трактор, но им понадобится только один бульдозер с функцией контроля уклона, который будет стоить примерно 1800 долларов для мобилизации на стройплощадке — экономия 360 долларов.
- Расчистка площадки —При расчистке площадки для строительства без контроля уровня требуются пределы разбивки рабочих, чтобы обеспечить соблюдение контрольных точек на протяжении всего процесса очистки площадки.Благодаря системе контроля уклонов контрольные точки легко проверяются за счет внедрения технологии топо, что позволяет подрядчикам экономить около 1440 долларов на трудозатратах.
- Вскрытие верхнего слоя почвы —При выемке верхнего слоя почвы без контроля качества требуется рабочий для проверки измерений, что обходится подрядчикам примерно в 2400 долларов.
Система контроля высотных отметок гарантирует, что почва очищается с точными размерами, основанными на топологии, интегрированной в систему, что позволяет подрядчикам экономить на трудозатратах.
- Вырубка / насыпь —Без контроля уклона для выполнения задания по выемке и насыпи требуются два ADT, один экскаватор, два бульдозера, один трактор, один рабочий и шесть операторов — это обходится подрядчикам примерно в 294 000 долларов. Для контроля уклона требуется только один бульдозер, без рабочего и всего пять операторов, что дает ориентировочную стоимость выемки и насыпи в 236 000 долларов — экономия в 58 000 долларов.
- Укладка заполнителя / камня —Для размещения заполнителя и камня два оператора потратят около 320 часов на нанесение материалов на рабочую площадку без контроля уклона.Один трактор, один бульдозер и один рабочий потратят 160 часов на выполнение части проекта по размещению агрегатов. Система контроля уклона позволяет двум операторам тратить на проект 224 часа, а на 112 часов требуются только бульдозер и трактор.
Без необходимости в рабочем, контроль успеваемости позволяет сэкономить около 288 проектных часов, а общая экономия составляет 30 720 долларов.
- Повторная заделка верхнего слоя почвы — С контролем высотного слоя меньше операторов и рабочих не требуется для завершения повторной заделки верхнего слоя почвы.Бульдозер с функцией контроля высотной отметки будет тратить половину времени на повторное разравнивание верхнего слоя почвы на бульдозере без контроля высотной отметки, что дает приблизительную экономию в размере 11 600 долларов США.
В целом контроль содержания может сэкономить подрядчикам на проектах примерно 118 520 долларов. С экономией на рабочей силе и затратах на оборудование пора подумать о бульдозере с функцией контроля уклона для вашего парка.
На основе этого примера проекта подрядчики, которые обходятся без контроля качества, могут даже не иметь шанса заключить контракт.Возврат инвестиций очевиден на протяжении всего процесса. В среднем система управления трехмерной машиной стоит от 60 000 до 70 000 долларов, а базовая станция, ровер и сборщик данных — примерно 30 000 долларов. Один проект с контролем успеваемости может окупить себя.
Контроль качества быстро растет с внедрением интегрированных систем. Хотя начальная цена может напугать людей, соблюдение процесса контроля качества может сэкономить подрядчикам тысячи долларов в плане их чистой прибыли.
Введение в систему управления станками с ЧПУ
Недавно мы дали вам несколько советов по покупке вашего первого фрезерного станка, но мы не коснулись систем ЧПУ (числового программного управления) для фрезерных станков (или других станков, например токарных). Это потому, что ЧПУ — сложная тема, и она заслуживает отдельной статьи. Итак, сегодня мы подробно рассмотрим, что такое ЧПУ, как оно работает и, в конечном итоге, подходит ли оно вам как любителю.
Краткая история ЧПУ
Как читатель Hackaday, вы, без сомнения, технически подкованный человек, который уже хоть немного знаком с концепцией ЧПУ. В конце концов, это просто автоматизация обработки по своей сути. Как и следовало ожидать, история систем ЧПУ довольно точно отражает развитие компьютеров, и они напрямую связаны между собой. Первые полностью автоматизированные системы управления начали появляться в 1950-х годах с числовым программным управлением (NC). Они использовали перфорационные ленты (или аналогичные методы хранения инструкций) для управления станками — в основном фрезерными станками, маршрутизаторами и токарными станками.
Подача энергии для этих машин уже давно существует.Они использовали (и до сих пор используют) электродвигатели или механические звенья для подачи определенной оси на станке с постоянной скоростью. Выгоды были двоякими: это было намного меньше труда для машиниста, а плавная и постоянная подача улучшила качество поверхности и срок службы инструмента.
К 50-м годам у высокопроизводительных станков были более совершенные средства управления подачей мощности, которые можно было настроить на разные скорости. Числовое управление по сути просто автоматизировало существующую технологию. Операторы могли указывать станку, когда и куда перемещать каждую ось, тем самым удаляя наиболее трудоемкую часть обработки (точный поворот рукояток).
Эта технология развивалась довольно предсказуемо: цифровые компьютеры привели к появлению ЧПУ, устраняя необходимость в устаревших перфолентах. CAD (автоматизированное проектирование) пришло и сделало процесс проектирования цифровым, дав операторам возможность проектировать деталь и программировать машину на компьютере. Компьютеры стали в геометрической прогрессии меньше, мощнее и дешевле. Усовершенствована электроника машины, что позволило повысить точность управления и улучшить обратную связь.А недавно движение за открытый исходный код, в частности, сделало станки с ЧПУ доступными для любителей.
Преимущества ЧПУ
Наиболее очевидным преимуществом ЧПУ, особенно в производстве, является автоматизация. Если производителю необходимо изготовить тысячи идентичных деталей, процесс CAD и CAM (автоматизированное производство) необходимо выполнить только один раз. Затем один оператор может одновременно управлять несколькими машинами, просто загружая и выгружая детали и нажимая кнопку «Пуск».«Эта эффективность привела к возможности массового производства сложных обрабатываемых деталей (то, что делалось вручную в первой половине 20 века) с впечатляюще высокой точностью.
Еще одно ключевое преимущество ЧПУ — точность и повторяемость. Точность всегда была важной частью обработки, но выдерживать жесткие допуски при ручном управлении станком непросто. Это требует от машиниста хороших математических навыков, знания машины и особого внимания к деталям.Если машинист повернет ручку на несколько градусов слишком далеко, деталь может потребоваться утилизировать, поскольку она не соответствует допускам, требуемым инженером.
С другой стороны, станки с ЧПУ очень хороши в математике. Они точно знают, где должны быть расположены, и могут безупречно повторять свои программы снова и снова. После того как программа обработки детали была усовершенствована программистом ЧПУ, производитель может быть уверен, что все детали будут идентичны друг другу.Пока станок работает правильно и инструмент в хорошем состоянии, программа отдельной детали может выполняться бесконечно долго с идеальными результатами.
Еще одно преимущество, которое часто упускается из виду, но которое чрезвычайно важно в нашем современном мире, заключается в том, что станки с ЧПУ способны совершать движения, которые люди не могут воспроизвести. В качестве примера возьмем простой круглый карман. В наши дни это настолько тривиально, что мы даже не задумываемся об этом — фрезерный станок с ЧПУ может резать его разными способами, используя любой инструмент, диаметр которого меньше диаметра кармана.Но для того, чтобы вручную обработать такой же карман, машинисту потребуется либо отверстие с точно таким же диаметром, что и карман, либо поворотный стол для вращения детали. И последнее потребует, чтобы ось поворотного стола была точно выровнена с осью кругового кармана.
Это потому, что круг требует одновременного перемещения двух осей с разной скоростью по отношению друг к другу. Машинист просто не может сделать это вручную, по крайней мере, при сохранении каких-либо реалистичных допусков.Думайте об этом, как о попытке нарисовать идеальный круг на Etch A Sketch, а теперь представьте, что вам нужно сделать это с допусками менее одной тысячной дюйма. Это просто невозможно сделать вручную, но на фрезерном станке с ЧПУ это легко сделать.
Пример детали, которую было бы невозможно обработать без ЧПУ (фото любезно предоставлено HAAS)Эта же концепция получает дальнейшее развитие, когда формы становятся более сложными, и когда вы добавляете третью, четвертую, пятую или шестую оси . Многие из продуктов, которые мы сейчас считаем само собой разумеющимися, просто было невозможно производить до появления ЧПУ, потому что их нельзя было обрабатывать вручную.
Фрезерный станок с ЧПУ не заботится о том, движется ли он просто по прямой по одной оси или координирует движение по шести осям одновременно. Конечно, программа обработки деталей становится больше, но с современными системами хранения и обработки это больше не проблема.
Типы систем ЧПУ
Основными типами ЧПУ являются двух- или трехосные системы, предназначенные для модернизации ручных станков. Они бывают разных типов как для фрезерных, так и для токарных станков и по сути просто объединяют компьютер и механическую подачу.Компьютер контролирует подачу мощности для каждой оси и пытается компенсировать люфт в каждой оси. Эта компенсация осуществляется либо по замкнутому, либо по разомкнутому циклу.
В системе ЧПУ с открытым контуром обратной связи нет. Сигналы отправляются только в одну сторону, и компьютер не знает, правильно ли то, что машина на самом деле делает. Он просто полагается на машину, чтобы делать то, что она должна делать. Люфт компенсируется фиксированной величиной, поэтому его необходимо знать заранее.Так работают самые недорогие станки, и обычно они дают хорошие результаты. Однако отсутствие обратной связи означает, что люфт обычно не устраняется идеально, и поэтому может быть трудно выдерживать жесткие допуски.
используют энкодеры для обеспечения обратной связи с компьютером. Это означает, что такие вещи, как люфт, можно автоматически компенсировать — компьютер просто проверяет, перемещается ли ось на желаемую величину, и соответствующим образом корректирует, если это не так. Однако системы с обратной связью требуют дополнительного оборудования и более сложных управляющих компьютеров, и поэтому они более дороги.
Основной альтернативой модернизированным системам, конечно же, являются станки, разработанные с нуля для управления с помощью ЧПУ. Так строится большинство современных машин, так как они могут включать множество дополнительных функций, которые необходимы. К ним относятся устройства смены инструмента, автоматизированные системы подачи СОЖ, дополнительные оси (для вращения детали, обработки под углом и проникновения в полости), продвинутые шпиндели и многое другое. С помощью специальной машины все это также может быть красиво упаковано в корпус, содержащий охлаждающую жидкость и стружку.
Как модифицированные, так и специализированные станки обычно имеют два метода создания программ обработки деталей: G-код и диалоговый. Режим G-кода принимает инструкции, созданные на отдельном компьютере (либо с помощью программного обеспечения CAM, либо написанные вручную), и запускает их точно так, как они написаны. В режиме разговора все это делается на управляющем компьютере, что позволяет оператору создавать программы прямо на станке.
Преимущество диалоговых режимов заключается в том, что оператор может быстро создавать простые программы без необходимости привлечения программиста с ЧПУ с использованием программного обеспечения CAD / CAM.Обратной стороной является то, что программы обычно упрощены, и создание сложных частей становится очень громоздким. Диалоговые программы также почти всегда имеют размер только 2.5D, что означает, что ось Z не может перемещаться одновременно с осями X или Y. Создание G-кода из программного обеспечения CAD / CAM позволяет вам взять сложную 3D-модель и напрямую создать для нее программу обработки детали, поэтому практически нет ограничений на сложность программы. Большинство современных мастерских будут использовать комбинацию этих двух методов в зависимости от необходимости, но любителям, вероятно, будет удобнее проектировать детали в CAD и использовать CAM для создания G-кода.
Рабочий процесс ЧПУ
Управление разговором может немного отличаться в зависимости от производителя и модели, и большинство из вас, вероятно, в любом случае заинтересуются проектированием деталей в САПР. Итак, мы собираемся сосредоточиться на методе G-кода для запуска станка с ЧПУ. Этот процесс очень похож на 3D-печать (которая также использует G-код), при этом программное обеспечение CAM заменяет программное обеспечение для резки 3D-печати.
Рабочий процесс начинается с создания 3D-модели вашей детали в САПР, уделяя особое внимание точности всех ваших размеров.Лучше использовать параметрическое программное обеспечение САПР, разработанное для машиностроения, в отличие от инструментов трехмерного моделирования произвольной формы, таких как Blender. Получив 3D-модель, вам нужно будет обработать ее в CAM, чтобы создать траектории инструмента, а затем вывести G-код. Большинство современных CAD-систем имеют интегрированное программное обеспечение CAM, а также доступно автономное программное обеспечение CAM. Однако это программное обеспечение обычно очень дорогое. Autodesk Fusion 360 — хороший бесплатный (для любителей) вариант, который имеет как CAD, так и CAM профессионального качества.
Когда вы переключаетесь на CAM, вам сначала нужно настроить деталь, чтобы сообщить станку, как деталь будет ориентирована, какой размер заготовки и как деталь будет расположена внутри этой заготовки. Если деталь необходимо переориентировать (например, для фрезерования дна), вам потребуется создать несколько настроек для каждой операции. Вам также потребуется настроить библиотеку инструментов, в которой будут определены доступные инструменты (концевые фрезы, сверла и т. Д.) И их размеры.
Следующим шагом будет создание траекторий инструмента для вырезания элементов детали. В отличие от 3D-печати, где модель просто нарезается на слои, траектории инструмента с ЧПУ должны создаваться вручную. Вам будет предложено множество различных вариантов траекторий инструмента, таких как контуры (для вырезания двухмерного профиля), торцевание и различные методы трехмерного контурирования. Требуется большой опыт, чтобы понять, какие типы траекторий использовать, но вы обнаружите, что очень часто используете несколько.
При создании траектории инструмента вам будет предоставлен ряд опций и параметров для определения.Это такие вещи, как какой инструмент использовать, скорость шпинделя, скорость подачи, глубина резания, шаг шага и так далее. Опять же, это требует большого опыта, но есть ряд инструментов, таких как HSM Advisor, которые могут помочь вам с этими настройками. Как правило, вам нужно найти баланс между временем, качеством и стойкостью инструмента. По этой причине очень часто выполняются быстрые и тяжелые черновые проходы для удаления большого количества материала за короткое время, а затем легкие чистовые проходы для точного удаления последней небольшой части материала с хорошей обработкой поверхности.
Создание траекторий инструмента — это то, на что вы, скорее всего, потратите большую часть своего времени, и важно сделать это правильно, чтобы не тратить материал на плохие программы обработки деталей, сломать инструменты или, возможно, даже повредить ваш станок. По этой причине всегда рекомендуется запускать встроенное моделирование, чтобы убедиться, что резка выполняется ожидаемым образом и что нет коллизий. Обратите особое внимание на то, где будут находиться ваши приспособления, тиски и стол, и чтобы инструмент не столкнулся ни с одним из них.
Autodesk Fusion 360 предлагает CAM профессионального уровня. Убедившись, что все траектории правильно настроены, вам нужно будет запустить постпроцессор, чтобы создать G-код для запуска вашей машины. G-код довольно стандартизирован, но у большинства машин есть собственный способ интерпретации кода. Таким образом, постпроцессор действует как посредник между программным обеспечением CAM и ЧПУ и обеспечивает совместимость выходного G-кода с вашим станком. Большинство программного обеспечения CAM будет иметь довольно обширную библиотеку постпроцессоров, и, вероятно, ваш ЧПУ уже там.В противном случае поиск в Интернете вашего CAM и ЧПУ позволит вам найти совместимый постпроцессор (или общий может даже подойти).
Имея G-код под рукой, вам нужно будет загрузить его в память вашего ЧПУ. Это в значительной степени зависит от используемой вами системы ЧПУ. Некоторые позволят вам просто загрузить его с USB-накопителя или по сети, в то время как другие старые элементы управления могут потребовать, чтобы вы загрузили его через последовательное или параллельное соединение. Но, как только G-код находится в памяти, большинство из них предоставит вам визуализацию траекторий инструмента, которую вы можете проверить, чтобы убедиться, что все выглядит правильно.
После загрузки материала в станок важно точно установить исходную точку по осям X, Y и Z. Это должно совпадать с настройками в программном обеспечении CAM. Обычно вы используете угол приклада или определенную точку на тисках / приспособлении. Важно то, что это реальный момент, на который вы можете сослаться. Когда все готово, вы можете нажать большую привлекательную кнопку «Пуск» и позволить машине приступить к работе.
Не удивляйтесь, если вы сломаете инструмент или у вас плохая отделка поверхности.Все это требует обучения, и хороший дизайн — это всегда повторяющийся процесс. Обладая достаточным опытом, вы начнете узнавать, какие настройки работают лучше всего и как производить детали высокого качества. Итак, наслаждайтесь процессом обучения и наслаждайтесь тем фактом, что вам больше не нужно часами вертеть ручки!
Охрана машин | Окружающая среда, здоровье и безопасность
Обзор
Движущиеся части машины могут привести к серьезным травмам на рабочем месте, таким как раздробление пальцев или рук, ампутации, ожоги или слепота.Ампутации, рваные раны и ссадины обходятся дорого и могут увеличить компенсационные выплаты работникам. (Ампутация — один из самых тяжелых и вредных видов травм на рабочем месте, часто приводящий к необратимой инвалидности. ) В связи с этим OSHA (Управление по охране труда и технике безопасности) установило ряд стандартов в отношении защиты машин. Защита машины предназначена для защиты оператора машины и других сотрудников в рабочей зоне от опасностей, возникающих во время нормальной работы машины.Это может включать опасные факторы, вызывающие озабоченность, такие как: точки входа в зону контакта, вращающиеся детали, возвратно-поступательное движение, поперечное перемещение и / или летящие стружки и искры.
Любая часть машины, функция или процесс, которые могут вызвать травму, должны быть защищены. Если работа машины или случайный контакт с ней могут привести к травмам оператора или других людей, находящихся поблизости, необходимо либо контролировать, либо устранять опасности.
Где возникают механические опасности
Опасные движущиеся части требуют защиты, потому что эти три области машины могут стать причиной травм:
- Точка операции
Точка, где с материалом выполняются работы, такие как резка, формование, растачивание или формовка заготовки. - Устройство передачи энергии
Все компоненты механической системы, которые передают энергию части машины, выполняющей работу. Эти компоненты включают маховики, шкивы, ремни, шатуны, муфты, кулачки, шпиндели, цепи, кривошипы и шестерни. - Другие движущиеся части
Все части машины, которые движутся во время работы машины. Они могут включать возвратно-поступательные, вращающиеся и поперечно движущиеся части, а также механизмы подачи и вспомогательные части машины.
Опасные механические движения и действия
Основными видами опасных механических движений и воздействий являются:
Движение:
Вращающийся (включая рабочие точки зажима)
Действия:
Раскрой
Движение:
Возвратно-поступательный
Действия:
Пробивка
Движение:
Поперечный
Действия:
Резьбовая гибка
Требования к охране
Охранники должны соответствовать следующим минимальным общим требованиям:
- Предотвратить контакт
Защитное ограждение должно предотвращать соприкосновение рук, предплечий и любых других частей тела оператора с опасными движущимися частями. - Secure
Операторы не должны иметь возможности легко снимать или изменять защиту. Ограждения и предохранительные устройства должны быть изготовлены из прочного материала, выдерживающего условия нормальной эксплуатации. Они должны быть надежно закреплены на машине. - Защищать от падающих предметов
Защитное ограждение должно гарантировать, что никакие предметы не могут упасть на движущиеся части. - Не создавать новых опасностей
Ограждение не может создавать опасности, такие как точка среза, зазубренный край или незавершенная поверхность, которые могут вызвать порезы. - Не создавать помех
Любое ограждение, мешающее оператору выполнять работу быстро и комфортно, вскоре может быть отменено или проигнорировано. - Обеспечьте безопасную смазку
Если возможно, операторы должны иметь возможность смазывать машину, не снимая защитные ограждения.
1. Стражи
Ограждения — это физические барьеры, которые закрывают опасные части машины и предотвращают контакт сотрудников с ними.Они должны быть прочными и закрепляться любым надежным способом, предотвращающим случайное смещение или снятие ограждения. Это предпочтительный метод защиты.
2. Защитные устройства
Защитные устройства — это элементы управления или приспособления, которые обычно предотвращают непреднамеренный доступ сотрудников к опасным участкам оборудования, если они правильно спроектированы и установлены. Примеры включают в себя: обнаружение присутствия, откат, удержание, средства безопасности и ворота.
Эти устройства могут выполнять одну из нескольких функций:
- Это может остановить машину, если рука или какая-либо часть тела случайно окажется в опасной зоне.
- Он может удерживать или вывести руки оператора из опасной зоны во время работы.
- Может потребоваться, чтобы оператор держал органы управления машиной обеими руками, чтобы не подвергать опасности обе руки и тело.
- Он может обеспечить барьер, который синхронизирован с рабочим циклом машины, чтобы предотвратить попадание в опасную зону во время опасной части цикла.
3. Вторичные методы защиты
Устройства защиты от обнаружения, устройства информирования, методы защиты и безопасные рабочие процедуры являются вторичными методами защиты.Эти методы обеспечивают меньшую степень защиты, чем основные методы защиты, поскольку они не препятствуют тому, чтобы сотрудники помещали или держали какую-либо часть своего тела в опасных зонах оборудования. Эти методы приемлемы только в том случае, если ограждения или предохранительные устройства не могут быть установлены по причинам невозможности. Вторичные методы защиты не должны использоваться вместо первичных методов защиты.
4. Расположение / расстояние
Чтобы часть машины была защищена местоположением, опасная движущаяся часть машины должна быть расположена так, чтобы эти области были недоступны или не представляли опасности для рабочего во время нормальной работы машины. Тщательный анализ опасностей для каждой машины и конкретной ситуации абсолютно необходим, прежде чем пытаться применить этот метод защиты.
5. Барьеры осведомленности (предупреждения)
Барьеры осведомленности не обеспечивают полной защиты от опасностей, связанных с машиной, они могут обеспечить оператору дополнительный запас безопасности. Барьер осознания не обеспечивает физической защиты, а служит только для напоминания человеку о том, что он приближается к опасной зоне. Как правило, информационные барьеры не считаются адекватными, если существует постоянное воздействие опасности.
Технический осмотр и обслуживание
Надлежащие процедуры проверки, технического обслуживания и ремонта в значительной степени способствуют безопасности обслуживающей бригады, а также операторов. Для обеспечения целостности оборудования и средств защиты оборудования необходимо разработать программу профилактического обслуживания, а не программу технического обслуживания после поломки, основанную на рекомендациях производителя и передовой инженерной практике.
Применимое постановление
29 CFR 1910, подраздел O и P
Требования к менеджменту (обязанности)
Обеспечьте надлежащие методы ведения домашнего хозяйства, обучение сотрудников / студентов и безопасные методы работы, поскольку они имеют решающее значение для создания безопасных условий труда вокруг оборудования.
1. Кафедры:
- Убедитесь, что машины оборудованы соответствующими защитными приспособлениями.
- Убедитесь, что Департамент охраны окружающей среды и безопасности RIT участвует в проведении оценки применимых машин / оборудования и их мер безопасности.
- При необходимости предоставьте операторам средства индивидуальной защиты (СИЗ).
- Устраните опасности поскользнуться, споткнуться и упасть в зоне, окружающей машины.
- Используйте поддоны при смазке оборудования.
- Удаляйте отходы по мере их образования.
- Сделайте рабочую зону достаточно большой для эксплуатации и обслуживания машины.
- Размещайте машины вдали от мест с интенсивным движением, чтобы не отвлекать сотрудников.
- Обеспечьте соблюдение требований к одежде, таких как запрет на свободную одежду, украшения или другие предметы, которые могут быть запутаны в механизмах, и длинные волосы следует носить под шапкой или иным образом удерживать, чтобы предотвратить запутывание в движущихся механизмах.
- Обеспечивает обучение операторов работе с машинами.
2. Руководители / специалисты цеха:
Убедитесь, что операторы не нарушают меры безопасности машины.
3. Механизаторы:
Работайте с машинами, соблюдая все меры безопасности.
4. Требования к обучению:
Инструктаж по безопасному использованию и уходу за машинами, а также обучение на рабочем месте под надзором необходимы для предотвращения травм. Только обученные сотрудники / студенты должны работать с оборудованием.
Обучение должно включать:
- Обзор мер безопасности, таких как: знание опасностей в рабочей зоне, включая опасности, связанные с машиной; порядок эксплуатации машины; процедуры блокировки / маркировки; и безопасные методы работы, такие как система напарников.